Production Capabilities
- Converting Capabilities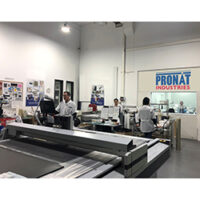
X-Y Flat-bed die-less cutting
XY flat-bed die-less cutting is a rapid and economic method for small and medium production runs. By substituting customers design files in place of expensive cutting dies, a rapid turnaround can be achieved and necessary changes can be easily incorporated as part of the process. The technology provides solutions for intricate, complex and multi-layer cutting of almost any thin or flexible material. It also offers highly accurate cutting tolerances without the need for investing in precise tooling. Rapid and economic solutions are available to support customers development projects through to mass production.
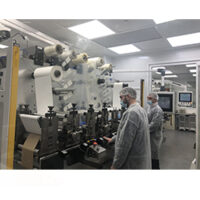
Rotary die-cutting
Rotary die-cutting with full servo-control, offers a most effective solution for both development and mass production of complex die cut parts, labels and laminations. This advanced rotary system is ideal for converting pressure sensitive adhesives, films, non-wovens, foams and fabrics. It offers an ideal platform for development projects for a variety of complex adhesive based die-cut components and disposable items.
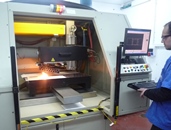
High speed laser cutting
High speed laser cutting enables the converting and production of highly complex parts at high speed and accuracy. The absence of any tooling, quick set-up and variety of sizes and suitable materials are just some of the benefits of this technology. We offer both flat-bed and reel to reel laser cutting with the option of an advanced vision system to enable cut to print.
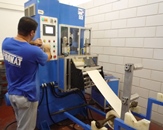
Flat bed die cutting
Flat-bed die cutting offers economic solutions for short runs and volume production of labels and adhesive based parts, especially where the parts are from thick materials and are large in size . This technology also permits prototype production runs to exact customer specifications and exacting tolerances.
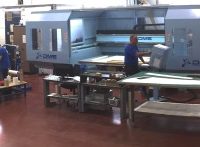
CNC Digital 3-axis routing
3-axis digital CNC routing enables accurate production of complex 3D components from technical plastics and rigid high density foams. Pronat’s engineering team can support customers in the selection of materials, the design of parts, and preparation of production codes (G-Codes), Quality inspection utilizing FARO 3D digital measuring arms are an essential part of this process.
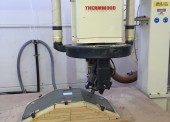
CNC Digital 5-axis routing
5-axis digital CNC routing permits the production of highly complex 3D components from technical plastics and rigid high density foams. Pronat’s engineering team can support customers with the selection of materials, the design of parts, preparation of highly intricate production codes (G-Codes) and the preparation of custom cutting jigs and molds. The quality inspection utilizing FARO 3D digital measuring arms are an essential part of this process.
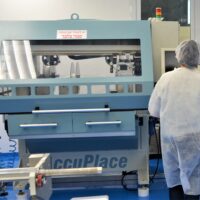
Pick & Place assembly
Highly accurate robotic pick and place technology provides unique adhesive assembly solutions not otherwise possible. Suitable applications include precise adhesive component positioning and highly accurate labeling. Pronat’s versatile equipment is available in both clean room and white room conditions and enables clients to undertake complex R&D and production projects with minimal lead time and low NRE investment.
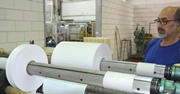
Slitting & sheeting
Pronat has decades of experience in precision slitting and sheeting. We offer reel to reel slitting with both duplex and single re-wind shafts and we can slit reels down to 5mm width. The company offers sheeting of films, adhesive rolls, label stock material, papers, foams and fabrics.
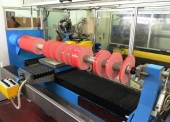
Lathe slitting
Precise lathe-slitting enables precise cutting of adhesive tape logs and foam rolls. In contrast to rotary slitters, lathe cutting permits the exact amount of material to be cut as necessary to suit the job, thereby eliminating unnecessary waste. The technology allows rapid set-up and enables the slitting of rolls up to 400mm diameter and tapes can be cut down to widths as thin as 2mm.
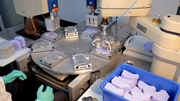
Ultrasonic & high frequency welding
Ultrasonic welding is one of the most effective methods of joining plastic materials. Pronat’s ultrasonic welding equipment is primarily used for the assembly of medical device components and in particular electrodes and disposables.
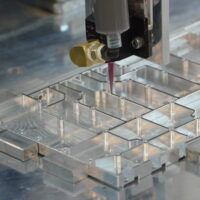
Form-in-place
Form in place technology is used for custom gasket shielding solutions by precise deposition of EMI paste. This system facilitates shielding where a standard EMI gasket cannot be fitted.